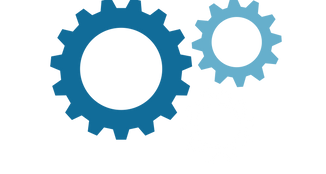
DYNAMIC IMPROVEMENT GROUP
INC.
What We Do

Leadership Development
Provide formal coaching and mentoring to BOD and C-suite levels, Plant managers, and shopfloor leaders in the organization.
Results in improved Policy Deployment, tactical leadership, revised KPIs, and standardized implementation processes. Significant reductions in cost, empowered teams, and achievements in sustainable growth. Operational leadership improvements in Operations and the Continuous Improvement organization.

Throughput Process Optimization
Focus on maximizing production throughput by analyzing current performance, identifying bottlenecks and non-value-added activities, and streamlining workflows.
Improves Throughput metrics, labor utilization, scrap, and changeover times.

Engineered Inventory for MRP Optimization
Analyze DOH inventory metrics and processes through standard organization, demand planning, engineered inventory calculator tools, automated inventory reports, and a cookbook methodology.
Significant results in net and gross inventory reductions, and corporate and plant level materials management competencies.

Labor Optimization
(Direct & Indirect)
Enhancing workforce efficiency by analyzing staffing levels, labor utilization, and material flow opportunities to eliminate non-value-added tasks.
Results in reduced costs, improved productivity, and better resource allocation, delivering measurable operational improvements. Clear definitions of direct and indirect VA.

Program Management
We ensure successful project execution by defining scope, managing timelines, and aligning resources to meet customer milestones. We provide cross-functional mentorship, risk management and APQP facilitation.
Deliver structured project timelines, controlled changes, and seamless launches.

Standard Problem Solving
Focusing on reducing downtime and improving quality systems by training teams in structured methods like PPS and A3. Using real-time data and cross-functional collaboration.
Delivers sustainable solutions, improved problem-solving skills, and a library of root cause examples, ensuring continuous improvement and operational excellence.
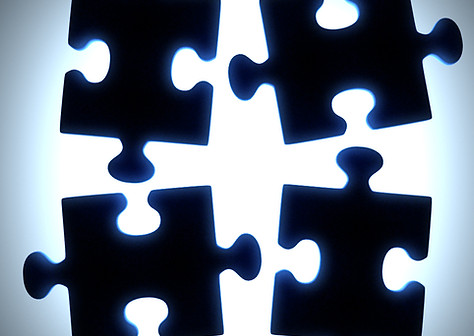
Quick Changeover
Reducing downtime and boosting efficiency by analyzing current changeover processes, training teams, and implementing tools like video analysis and pre-flight checklists.
Establishes new performance targets, standard work, and visual factory improvements, delivering faster changeovers, consistent quality, and cross-shift capability for enhanced operational agility.

Total Productive Maintenance
Enhancing equipment reliability and operational efficiency by implementing structured 7 Pillar maintenance practices, training teams, and engaging colleagues in continuous improvement.
Improves OEE, MTBF, and MTTR metrics, delivering sustainable performance gains, reduced downtime, and a standardized "cookbook model" for scalable TPM implementation across operations.

Production Preparation
Process (3P)
Optimizing future state layouts by integrating cross-functional teams, customer demand data, and lessons learned. Workshops focusing on reducing waste, improving flow, and right-sizing capital and labor for future projects.
Delivers efficient layouts, optimized cycle times, and flexible manning to meet customer demands effectively.

CI Organizational Development
Strengthening continuous improvement capabilities by assessing current structures, skills, and leadership gaps and taking them to the next level by our expert team members.
Designs future state plans, standardizes CI roles, and implement training, delivering enhanced CI direction, active corporate engagement, and measurable productivity improvements through optimized labor and changeover processes.
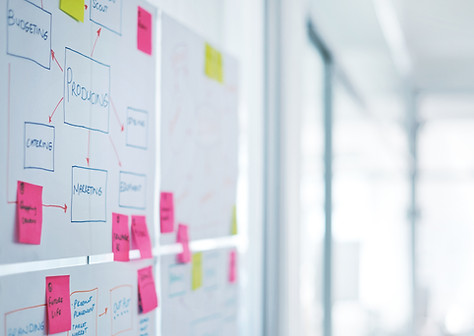
Six Sigma Variation
Reduction Training
Leading high-potential candidates with DMAIC methodologies and tools to identify and eliminate root causes of variation by providing certified green/black belt training and practical coaching and experience.
Delivers sustained process improvements, enhanced quality, and measurable SQDCM results, driving customer satisfaction and operational excellence. Formal Black belt and Green belt certification available.

Controls / Robotics
Support Competencies
Enhancing operational efficiency by optimizing PLC, HMI, robotics, and safety systems through tailored projects, training, and standardized practices.
Reductions in cycle times, downtime issues, and strengthens in-house capabilities, delivering improved performance, and cross-shift expertise. Ensures future-ready control standards for Industry 4.0 integration.

Data Enablement
Transforming raw data into actionable insights by ensuring accuracy, accessibility, and reliability.
Empowers teams with self-service analytics, enhances decision-making, and integrates data into the company culture. Delivers improved efficiency, informed leadership, and a robust framework for continuous operational improvement.

Executive Recruiting
& Placement
We make sure you have the right leadership fit by leveraging a network of vetted candidates and aligning with company goals, culture, and values.
Reduces hiring risks, provides confidential support, and delivers a tailored transition plan, enabling successful integration of specialized expertise into the organization.
