
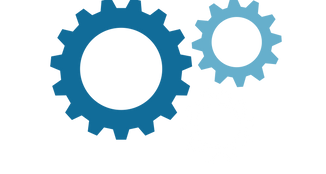
DYNAMIC IMPROVEMENT GROUP
INC.
Direct Labor Optimization
During this engagement, we conducted a value stream map and structured labor and waste assessment for the client. These tools identified significant inefficiencies in direct labor utilization, part presentation, line balancing, and non-value-added activities. Our diagnostic revealed clear opportunities to optimize staffing, reduce cycle times, and improve overall productivity while maintaining operational performance.
Current State Analysis (VSM)
We conducted an initial evaluation using Value Stream Mapping (VSM) to identify inefficiencies in direct labor utilization. Our structured approach rigorously analyzes current state operator tasks, machine cycle times, and material flow ensuring data accuracy and actionable insights. This method delivers a thorough diagnostic, establishing a foundation for sustainable labor productivity improvements.

Opportunities and Solutions
Initial staffing of 198 operators exceeded the required 147. Staffing was reduced by 51 operators by:
-
aligning labor to the correct Takt Time
-
significantly improving material flow and layout
-
optimizing material delivery and part presentation to the production line
-
establishing standard work for operators, team leaders and supervisors
-
eliminating manufacturing waste
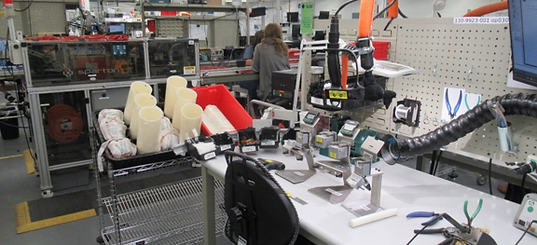
Demonstrated Hard Savings and Improvements
Through this labor optimization initiative, the client achieved $3.4M in annualized labor savings by reducing headcount by 26% without compromising output. Productivity improved through cycle time reductions and better workflow balance by aligning to a Takt time of 97.7 seconds per part. Additional benefits included lower overtime costs, fewer production delays, and improved on-time delivery—demonstrating the value of a structured workforce optimization approach.
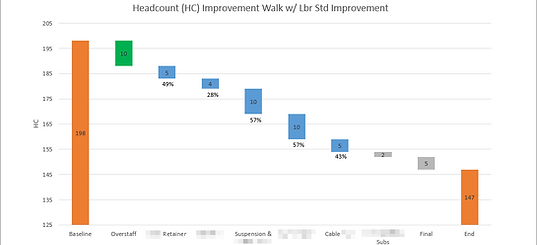