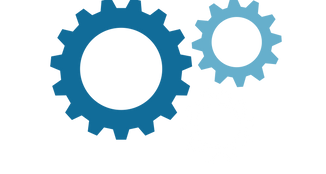
DYNAMIC IMPROVEMENT GROUP
INC.
What We Offer
We believe in teaching our audience (typically 90-120min) and then proceeding directly to the shop floor and applying the learned training immediately. This is then followed with another learning session, and another round of direct work application after. We continue this process of teaching and application until the training has been completed.
We are invested in being in the game, not on the sidelines,
& prefer to apply the training immediately after.
This allows for tangible benefits to your bottom line.
Training Modules
Standard Work
(Standard work for operators, team leaders, supervisors)
The process of Standard work is the foundation for having a Robust, Capable, and In Control shop floor process. This course is designed to achieve fundamental improvements from Standard Work line design, cell layouts, and operator value added work. The shop floor management team can support the production environment with good standard work methods as well.
Problem Solving
(Applied problem solving)
We believe problems are opportunities to make things better, and solving problems requires time and investment. In this training we use real life shop floor issues as practice to get to the root cause of an issue. We also focus on driving a common methodology and language to solve our problems, improving the skill sets of our human infrastructure, and standardizing our problem-solving process.
5s to Autonomous Maintenance
The foundation of every work space begins with understanding what things are, and where they belong. We want to involve and engage our colleagues in the continuous improvement cycle, and define better work standards for material, methods, and tools. Simply put, we must identify what we need and do not need, and then organize our cyclical needs for our operators to maintain our tools, inventory, and job aids. 5S is the beginning of Autonomous Maintenance for our colleagues to engage them in better line performance.
Shop Floor Pacing
(Hourly pacing)
Just by putting a shift schedule in front of our colleagues, and breaking it down into hourly expectations, we will see very quickly where our problems originate. By focusing on the CORE system of Operational Excellence, we can give our supervisors and operators a solid foundation for the regular discussions needed to improve.
Quick Changeover
(Single minute exchange of dies)
The changeover process is one of the most competitive performance measures we have available to us today. Reducing changeover time can improve our run rates, capacity planning, and inventory level. This course is geared to help with understanding the changeover process by definition and the background, history, and primary components of implementation. Covering traditional methods versus SMED, with focus on simultaneous and streamlined activities.
Zone Control
Our goal should be to never let any product out of our department, area, or work cell unless it is 100% acceptable to our next customer. For us on the shop floor this includes a high level of ownership for passing on a bad product to our internal and external customers. This course establishes and develops feedback mechanisms to our colleagues, so that we can pinpoint defects and scrap generation at the source.
Kaizen Workshop
After completing reviews of standard work methods to ensure opportunities, the team is introduced to the fast Kaizen approach involved in the workshop application. When we focus on a “lightning-fast” approach to moving and improving on the shop floor, we get everyone’s attention. It is important to understand how this cross-functional approach includes everyone on the shop floor.
Preventative Maintenance
(Preventative and predictive maintenance)
This training focuses on the commitment of maintenance and its three distinct phases. The first being related to the repair process or crisis management. The second involves a determination of the need for maintenance, using preventative measures. The third phase embraces predictive maintenance tools.
Value Stream Mapping
The value stream mapping process teaches us how to do a before and after characterization of our actual current state and estimates a future state of improvement to the system. In using this process we are able to highlight cycle quantities greater than needed, excessive repairs, and scrap and processing. Historically value stream mapping has driven scheduling improvements, manpower adjustments, and layout improvements.